Fabric inspection is an essential step in the textile industry as it ensures that fabrics meet the necessary quality standards and specifications before they are used in manufacturing. Fabric inspection is a comprehensive process that involves several steps to ensure that the final product meets the required standards.
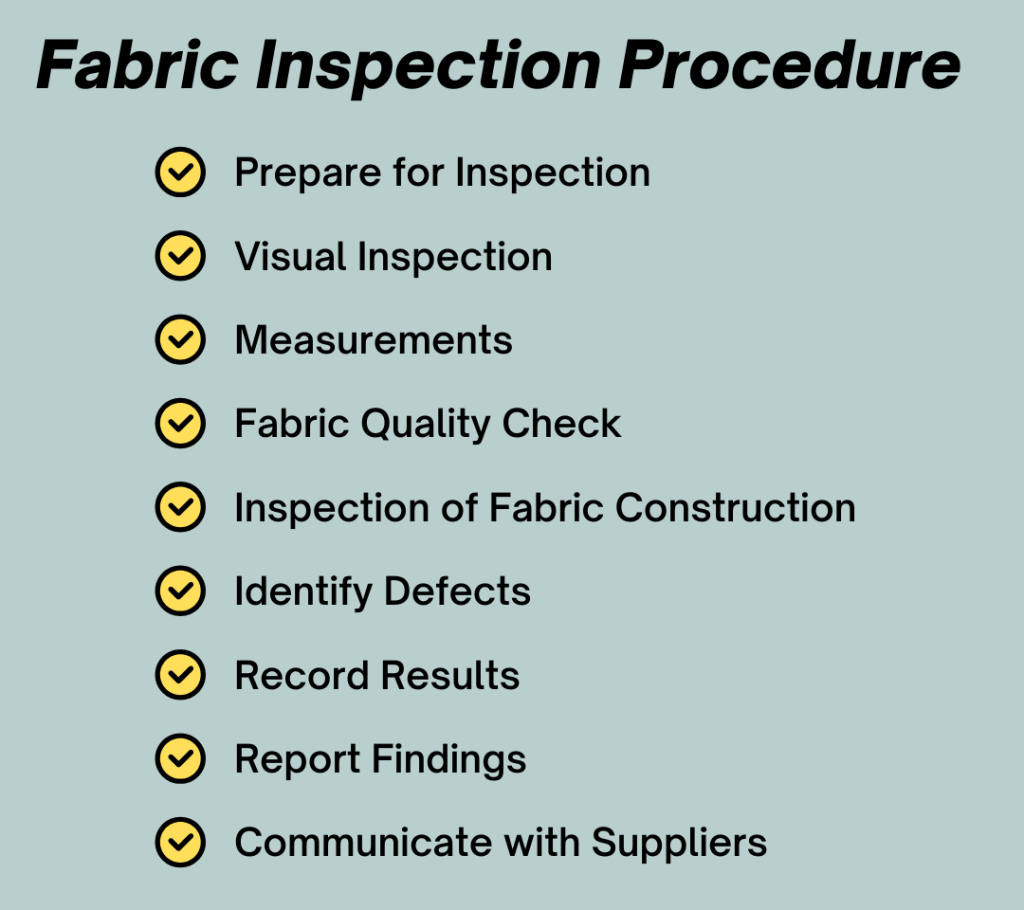
Fabric Inspection Procedure
1. Prepare for Inspection
Before starting the inspection, it is important to make sure that you have all the necessary tools and equipment. This may include a fabric inspection checklist, a light box, a ruler or measuring tape, and any other equipment required to perform specific tests. Make sure that the area where the inspection is taking place is clean, well-lit, and free of dust or other contaminants.
2. Visual Inspection
A visual inspection is the first step in fabric inspection. Examine the fabric for any obvious defects such as stains, holes, tears, or loose threads. It is important to pay attention to the overall appearance of the fabric, including its color, texture, and patterns. In this step, it is important to examine the fabric from different angles, to ensure that all defects are detected.
3. Measurements
Measure the fabric for length, width, and weight, and compare the results to the specifications provided. Make note of any deviations. Measure the fabric multiple times to ensure accuracy and make sure that measurements are in line with the industry standards. It is also important to check for any skewing or bias of fabric.
4. Fabric Quality Check
Check the fabric quality such as thread count, strength, shrinkage, color fastness, and hand feel. The thread count refers to the number of threads per square inch, and a higher thread count generally indicates a higher-quality fabric. Strength is measured by how well the fabric withstands various types of stress, such as tension, stretching or abrasion. Shrinkage is the change in the size and shape of the fabric after it has been washed, and color fastness is a measure of how well the fabric retains its color after it has been washed or exposed to light.
5. Inspection of Fabric Construction
Look at the fabric construction, check the weave, knitting and other details such as yarn size and type, fabric weight, and finish. It’s important to check the fabric for any inconsistencies or defects that might affect the quality of the final product. This includes checking for any missing or broken yarns, loose or tight threads, and any other issues that might affect the durability and appearance of the fabric.
6. Identify Defects
Identify any defects found in fabric construction, defects found in visual inspection, defects found in measurements, and defects found in quality check.
It’s important to carefully note any defects found during the inspection, including their location, size, and severity. This will allow you to quickly address any issues and make any necessary adjustments to the fabric.
7. Record Results
Document any defects that were found during the inspection and take pictures if necessary. It’s important to keep accurate records of all defects, measurements, and other information collected during the inspection. This will help you to identify patterns or issues that might be affecting the quality of the fabric and make adjustments as necessary.
8. Report Findings
Prepare a detailed report of the findings, including any defects found, measurements taken, and any other relevant information. Share the report with the supplier or other relevant parties, including the production team, so that they can take appropriate action to correct any issues that were identified during the inspection.
9. Communicate with Suppliers
Share the inspection report with the supplier, discuss any issues and work together to correct them. It’s important to establish a good working relationship with your suppliers, as they play a crucial role in ensuring that the final product meets the required quality standards. Regular communication and collaboration can help to identify and address any issues that may arise.
Different Testing Requirements for Fabric Inspection
Several specific tests and measurements can be used during fabric inspection to ensure that the fabric meets the necessary standards. These may include:
- Abrasion resistance test: A test to measure the resistance of the fabric to abrasion or wear.
- Bursting strength test: A test that measures the strength of the fabric by applying pressure to the fabric until it bursts.
- Tearing strength test: A test that measures the strength of the fabric by applying a force to the fabric until it tears.
- Colorfastness test: A test that measures how well the fabric retains its color after being washed or exposed to light.
- Pilling test: A test that measures how resistant the fabric is to pilling, which is the formation of small balls of fiber on the surface of the fabric.
- Shrinkage test: A test that measures how much the fabric shrinks after being washed or exposed to heat.
- Stretch test: A test that measures how much a fabric can stretch without breaking or losing its shape.
- Dimensional stability test: A test that measures how well a fabric retains its shape after being washed or exposed to heat.
Conclusion
Overall, fabric inspection is a critical step in the textile manufacturing process that helps to ensure that the final product meets the necessary quality standards. By following a comprehensive inspection procedure and conducting the appropriate tests and measurements, manufacturers can identify and address any issues that may affect the quality of the fabric, ensuring that the final product is of the highest possible quality.
Good summary for fabric sop and its testing methods ,congratulations on this